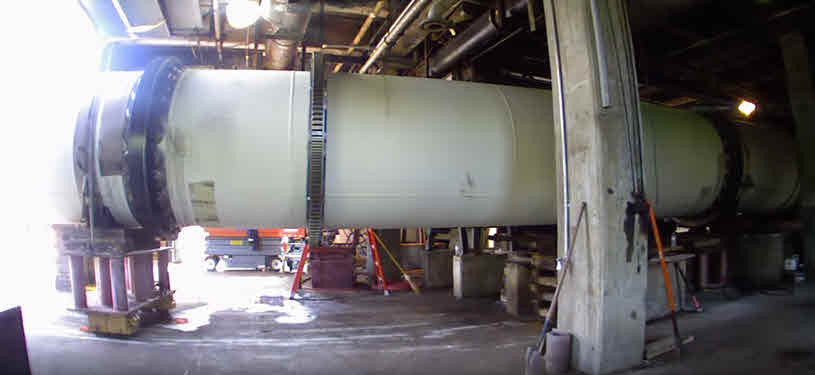
Each summer, most of the large whiskey distilleries shut down for summer maintenance for anywhere from four to six weeks. It’s a time for distillers to do routine maintenance, replace old equipment or to add new equipment to keep up with demand. It’s work that’s just not possible the rest of the year for these distilleries that are often operating six or seven days per week. After all, that fermenting mash doesn’t take the weekend off, it’s there round the clock for three to five days before it moves on to the distillation process.
This summer Buffalo Trace Distillery replaced one of its grain dryers that dated back to the 1950s. Removing the dryer and inserting the new one was no small feat. In order to install the new, 63,853 pound dryer, the Louisville Dryer Company had to hoist the massive dryer over the Kentucky River and into the Distillery’s Dryhouse, using a large crane.
Out with the Old Grain Dryer
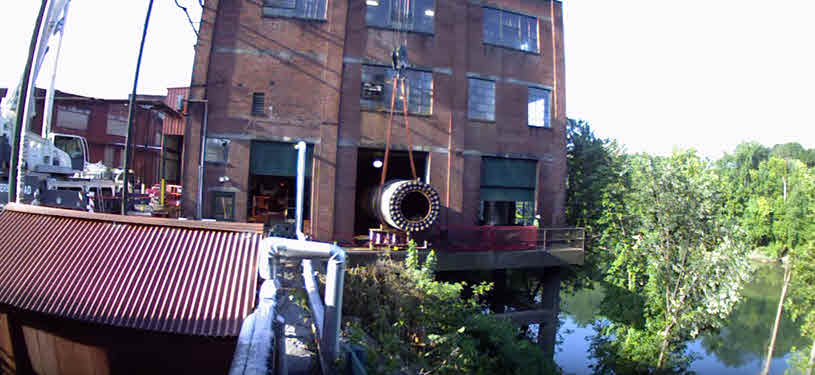
In with the New Grain Dryer
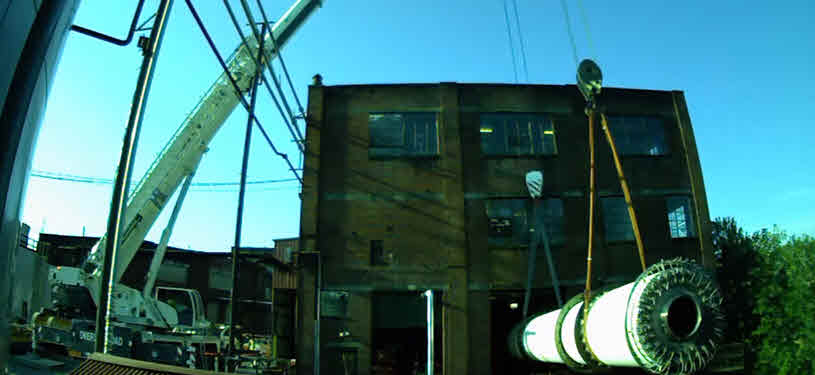
Stay Informed: Sign up here for the Distillery Trail free email newsletter and be the first to get all the latest news, trends, job listings and events in your inbox.
Now in place among four other dryers in use at Buffalo Trace Distillery, the new dryer, though the same size as the one it replaced, is capable of handling 30 percent more work. The distillery uses these grain dryers to dry the spent grains that were used in the whiskey-making process, then sees that all of its distilled dried grains are recycled and put to use in other ways.
Grains Come From the Farm, Grains Return to the Farm
The Distillery keeps its dryers busy six days a week to keep up with its bourbon production, and sends off roughly 750,000 pounds of distilled dried grains each week to local farmers who then reuse that dried grain for feeding livestock.
Kristie Wooldridge of Buffalo Trace Distillery said that 99+% of the dried grains are sent off to farms but a small percentage is sent to nearby Weisenberger Mills to be converted into food products. The mill, originally built in the 1800s and run by the sixth generation of Weisenbergers then converts that spent distiller’s grain into Buffalo Trace Biscuit Mix and Buffalo Trace Pancake Mix. Both products can be found in the distillery’s gift shop.
Looking for Grain Drying Solutions? Find Grain Drying Engineers and Equipment Providers in our Distillery Suppliers Directory.
Buffalo Trace Biscuit Mix and Buffalo Trace Pancake Mix

“Everything has a purpose around here,” Master Distiller Harlen Wheatley said. “Nothing goes to waste. Once our grains serve our intents in our whiskey making process we’re happy to be able to support our local farmers and give that spent grain another purpose.”
The new dryer installation took place during Buffalo Trace’s annual summer shut down, which typically lasts from about mid-June through the beginning of August. The Distillery uses that time to deep clean all facets of the distilling process and make necessary repairs in order to keep things running efficiently and to get the most use out of its equipment. It’s safe to say that each dryer at Buffalo Trace sees its fair use, as it still has two dryers in place that date back to the 1940s. These old faithful machines will likely be replaced in the coming years as well.
Here’s a time lapse video of the grain dryer removal and installation process as it occurred over a 14 day period.
Replacement of a 63,853 Pound Grain Dryer
Please help to support Distillery Trail. Sign up for our Newsletter, like us on Facebook and follow us on Twitter.