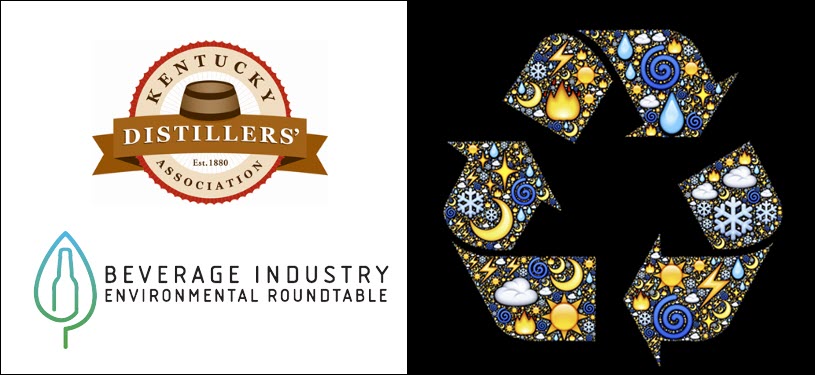
If you’ve ever visited a distillery you know that it’s an industrial process from start to finish. Making bourbon requires a lot of natural resources like corn, wheat, rye, malted barley and water – lots and lots of water. As the grains move through the distillery they will be ground, mixed with water and cooked. Different grains will be tossed in the cooker at different temperatures. After cooking, it’s time for fermentation. The mash has to be just the right temperature before adding the yeast. Too cold and the yeast will be held back. Too hot and the yeast could be stressed. After three to seven days, fermentation is complete and it’s time for distillation. Distillation is accomplished by heating up the mash until the temperature is hot enough to separate the alcohol into a vapor. Once it’s separated then it has to be cooled to turn it back into a liquid. You get the idea; distillation requires a lot of energy and a lot of water at every step of the process.
The Kentucky Distillers’ Association and it members make up to 95% of the world’s bourbon. With such great power comes great responsibility. Most often you’ll hear their responsibility efforts geared toward responsible consumption, in this case the Association members are taking a hard look at sustainability through responsible use of natural resources more specifically the use of water and energy.
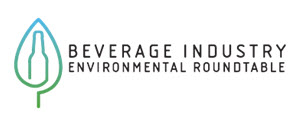
Four Roses, Heaven Hill, OZ Tyler, and Wild Turkey joined existing BIER members Bacardi, Beam Suntory, Brown-Forman, and Diageo in submitting data – ensuring the addendum represents 98% of KDA membership by production volume.
Andy Battjes, Brown-Forman’s Director of Environmental Health & Safety, was instrumental in initiating the partnership. “For Brown-Forman, one of the advantages of being a BIER member is learning from the technical expertise of other member companies and using that information to accelerate our own environmental sustainability improvements,” said Battjes. “We felt it was important to share this wealth of knowledge with our fellow Kentucky distilleries so we can continue working together to protect and sustain the natural resources that we all depend on and share.”
The results offer an insightful performance analysis of Kentucky’s distilleries, combining benchmarking data from KDA and BIER members to analyze Kentucky Bourbon distilleries’ efficiency when compared to global industry peers.
Overall, Kentucky distilleries’ collective energy and water use ratios consistently declined from 2013 to 2017, and rested below the global distillery averages in 2017.
Specifically, nine of the 11 participating Kentucky distilleries performed within the top 50% of global distilleries with regard to energy use ratio.
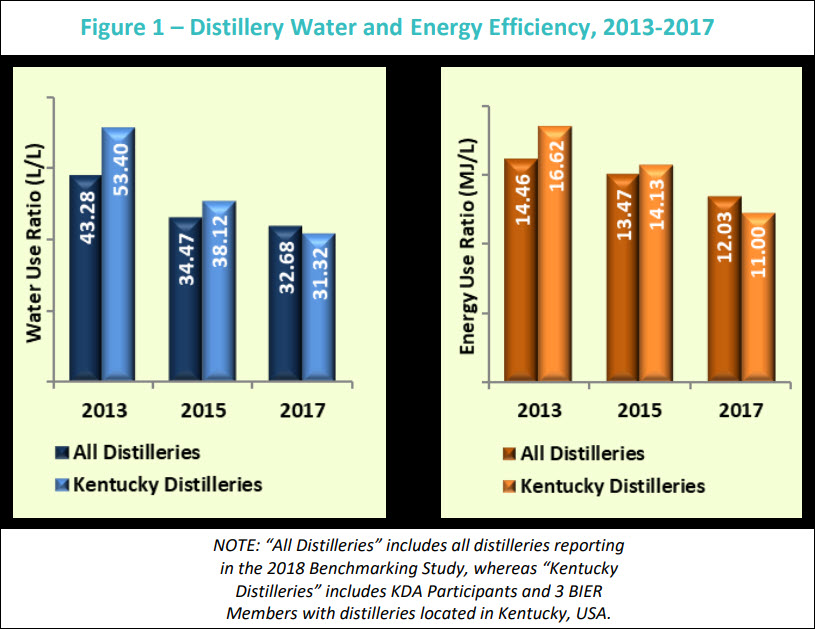
Heaven Hill Reduces Water Usage by 33% by Recycling Water
Heaven Hill Brands is a Kentucky Distillers’ Association member that was new to BIER’s environmental benchmarking study, and it presented some of the greatest efficiency improvement.
After updating the water source at its Bernheim Distillery in Louisville, Kentucky the company reduced its water usage by 33%. By placing two still condensers onto the cooling tower loop, the distillery now recycles water within its operations instead of sourcing it new – saving 330,000 gallons of water per day.
Historically, Heaven Hill Brands has tracked environmental information primarily to comply with regulatory requirements; however, in recent years, it has used data to make informed decisions on sustainability-related equipment purchases and process improvements.
Thanks to the study, the company has identified its environmental footprint, compared it to industry peers’, and discussed ways to strive for even greater efficiency moving forward.
Rhoneé Rodgers, the company’s Environmental Health & Safety Manager, said, “Participating in this study helped me understand the beverage industry’s impact on environmental sustainability. While Heaven Hill makes a direct impact locally, we make a greater difference when we work in conjunction with our colleagues across the industry. I feel good about what we have accomplished so far and will continue striving for this goal of environmental sustainability.”
Stay Informed: Sign up here for the Distillery Trail free email newsletter and be the first to get all the latest news, trends, job listings and events in your inbox.
Tracking Energy and Water Usage a Challenge for Craft Distilleries
Despite its success, Kentucky Distillers’ Association’s first environmental benchmarking study encountered challenges, too. Craft distilleries lacked the employee resources to track energy and water usage over the past five years, and larger distilleries struggled to quantify their Scope 1 and 2 emissions.
Moving forward, Kentucky Distillers’ Association will partner with BIER and local stakeholders like the Kentucky Energy & Environment Cabinet’s Division of Compliance Assistance to provide workshops that strengthen these capabilities amongst Kentucky’s distilleries.
The Kentucky Distillers’ Association and Beverage Industry Environmental Roundtable is expected to continue to be updated every other year.
A summary of the February 2019 Kentucky Distillers’ Association Drives Improvement in Water and Energy Efficiency Benchmarking Report can be found here.
Benchmarking Definitions & Methodology
To establish the benchmarking dataset, each company submitted three years (2013, 2015, 2017) of facility-specific data as described below. The definitions below are focus on distilled spirits but other studies from BIER also cover beer, wine and non-alcoholic spirits. The full report can be found here.
Total Water Usage: All water used by the plant (including Bottling and Industrial Water) from all sources used for activities including but not limited to: beverage production, cleaning/sanitizing processes, cooling waters, sanitation, landscaping, etc. Total Water Usage includes stormwater/rainwater captured for activities defined above. The scope of this study does not include water used to grow ingredients or at warehousing or office facilities. This definition is generally aligned with GRI Standard 303-1 (2016). Total Water Usage excludes Return Water.
Total Energy Consumption: All energy consumed on site from all sources used for activities including but not limited to: facility operation, beverage production, cleaning/sanitizing processes, bottling processes, pasteurization, cooling, sanitation, etc. This definition is generally aligned with GRI Standard 302-1 (2016).
Total Beverage Production: The volume of finished product generated at a facility or by a company. For facilities that produce alcoholic beverages, total beverage production should represent the actual volume of product (wine gallons) and should not be scaled to a specific alcohol content.
Water Use Ratio (L/L): Calculated as the ratio of Total Water Usage to Total Beverage Production and is an indicator of the efficient use of water by a company of facility.
Energy Use Ratio: A measure of efficiency defined on a Facility Specific or Company-Wide basis as Total Energy Consumption / Total Beverage Production. This definition is generally aligned with GRI Standard 302-3 (2016)
Beverage Facility Types: Four facility types were identified for the data collection process: Bottling Facility, Brewery, Distillery, and Winery. This study did not include warehouses, corporate offices, food products, glass shops, or malting operations.
Beverage Product Mix: A description of all Beverage Production Shares across a company or individual facility. The sum of Beverage Production Shares across an entity should equal 100 percent. For purposes of this study, ten beverage types were identified: beer, bottled water, carbonated soft drinks, distilled spirits (high-proof), distilled spirits (low proof), juice – not from concentrate, juice from concentrate, non-carbonated beverages, wine and other.
Please help to support Distillery Trail. Like us on Facebook and Follow us on Twitter.